Custom Designed Automated Vision Inspection System for the Automotive Manufacturing Industry
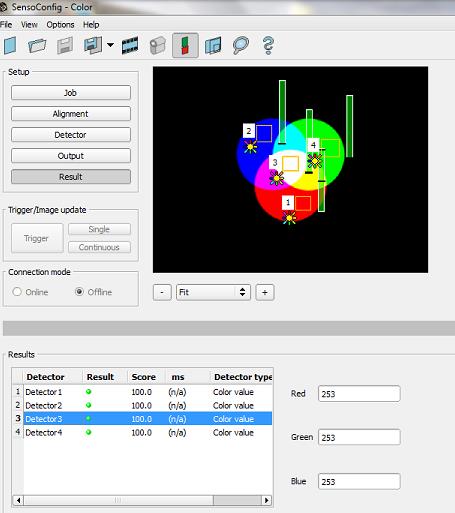
The vision system is programmed to look for specific characteristics. The system verifies these characteristics are present where they belong and also verify none are present where they don’t. By doing so it is capable of providing 100% verification of the specified characteristics. Each passing part is automatically marked with a quick dry ink for quality tracking purposes.
The customer had been using manual inspection of each part which was very time consuming and also made it difficult to maintain the zero error requirements their customer requires.
Project Description
This automated vision based inspection station verifies the correct assembly of every part manufactured.
Capabilities Applied/Processes
Cell Design
- Conception of cell that meets unique production requirements.
- Create SolidWorks© 3D models of cell concept
- Vision and lighting application concept and testing
Installation
Start-Up
Operator and Maintenance Training
Features/Benefits
Features
- Utilizes Teledyne Dalsa BOA color vision/li>
- Portable Cell/li>
- Provides visual and audible feedback on each part inspected./li>
- Capable of 30+ individual inspections per part./li>
- Multiple part types can be programmed and inspected.
Benefits
- By utilizing a color vision system and the correct lighting for the application it is able to compensate for color and finish variances that are not critical to the part quality test./li>
- Multiple parts can be programmed and accessed directly by the integrated operator HMI./li>
- Easily modified to meet new product requirements.
More Info
Overall Cell Dimensions
Table top unit: 39” High x 39” Wide x 39” Deep
Pattern Size Capabilities
50mm high by 300mm wide
Tightest Tolerances
1mm
Material Used
Glass beads
In Process Testing Performed
Samples of all models were provided for initial concept testing
Industry for Use
Automotive
Delivery Location
Ohio
Standards Met
Customer supplied part models
Product Name
Vision Based Automated Inspection System